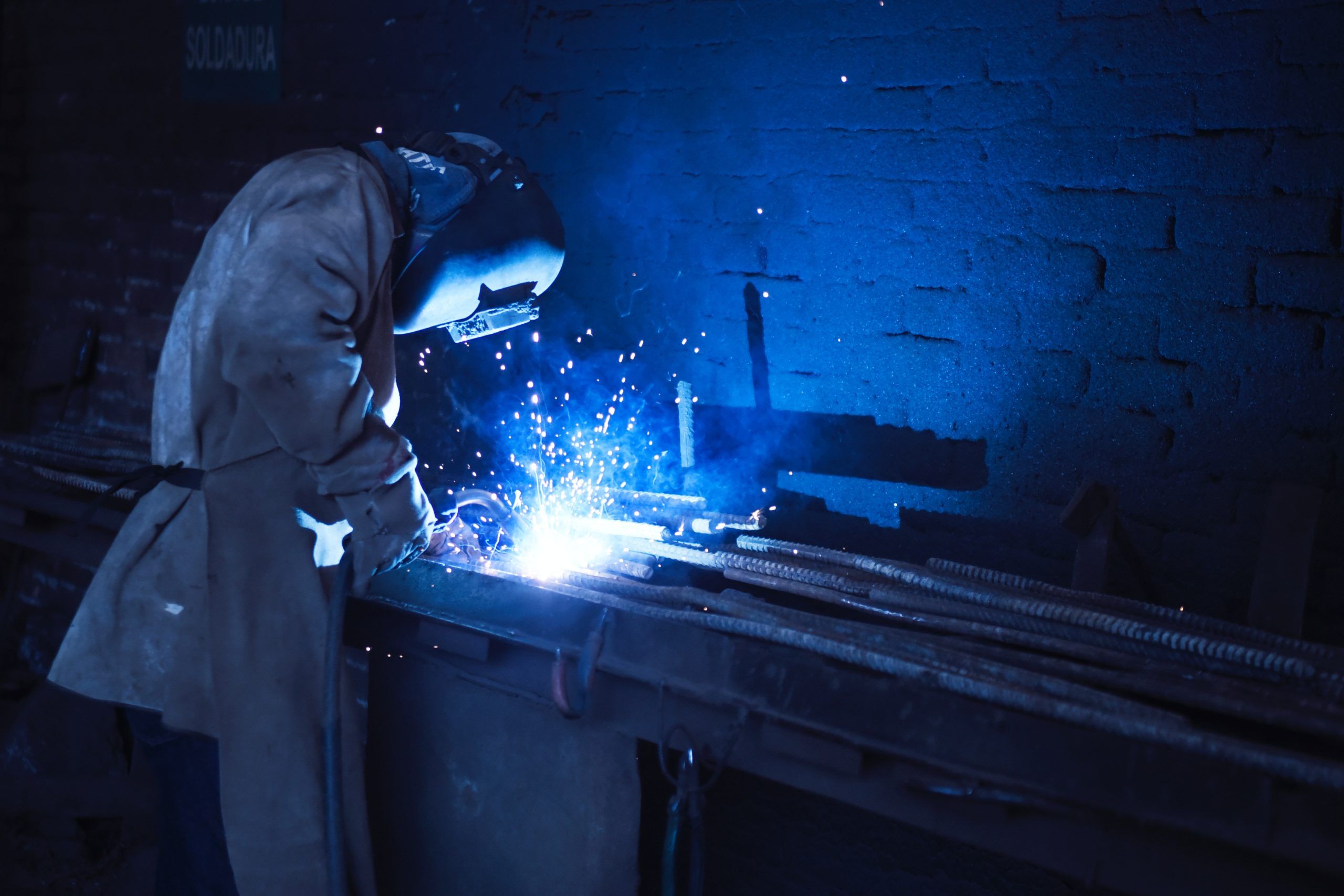
Have you ever stopped to think how many welds there are in the structure of your car?
What would happen if they weren't strong enough to withstand the knocks and wear and tear of time? Better not think about it.
Luckily, there are those who do it for us.
The solderability test is a laboratory test aimed precisely at ensuring the tightness of these and other welds.
Let's find out together.
What is the Solderability Test for
The solderability test is necessary to verify the behavior and tightness of all types of welds when subjected to mechanical stress and/or extreme environments.
As we have anticipated, the automotive sector is among the most interested in welding tests given the high number of welds involving the frame, the bodywork and the various engine components of a common automobile.
For the same reasons, in the aeronautical, naval and military sectors, engineers are required to conduct rigorous solderability tests in order to evaluate the tightness of the welds of vehicles which often have to withstand extreme stresses and unconventional atmospheric environments.
Perform
Extreme Testing
Discover the new series of Environmental Chambers for controlled climate testing
How the Solderability Test Works
The solderability test is actually a set of individual tests, mostly mechanical, which verify the seal of the weld to different types of stress
The tests that we generally find in the weldability test as prescribed by international standards are the following:
- Tensile test
- Bending test
- Flexing test
- Hardness test
Each of these tests subjects the weld to a different type of mechanical stress.
The welded sample is placed inside specific laboratory instruments designed for mechanical testing of materials which are capable of carrying out one or more tests of this type.
Which and how many tests need to be performed varies from sector to sector and from product to product.
The major international standards affecting solderability testing are the following: ISO 5817:2014, AWS D1.1:2015, MIL-STD-750 Method 2026, and J-STD-002.
Climatic Chambers and Solderability Tests
Solderability testing is mostly composed of mechanical testing, as we have seen, but climatic testing is not out of the picture.
As with many other tests on products and materials that are not directly climatic, in fact, it must be considered that there is no neutral environment and that each sample we test will have its life cycle in a specific atmospheric context.
In this sense, the solderability tests that establish the concurrence of climatic tests are those involving welds that will live in extreme environments such as those of the naval and submarine industry, exposed to a high risk of corrosion.
You cannot find the ideal chamber for your test?
Create your own environment, according to any test requirement
The FDM Climatic Chamber for the Solderability Test
For testing the resistance of welds and other materials to corrosion and, in general, to extreme environments, there is no better tool than an environmental chamber.
FDM environmental chambers are designed to perform all extreme climatic tests, including those affecting particularly sensitive sectors such as military aeronautics or marine engineering.
We can also design climatic modules to integrate with hydraulic presses for tensile tests. We've already done it for a client and we've told it here.
For further doubts and questions, please do not hesitate to contact us.
Would you like to receive a quote or do you have questions about the product?
Contact us to receive more information about this Product.