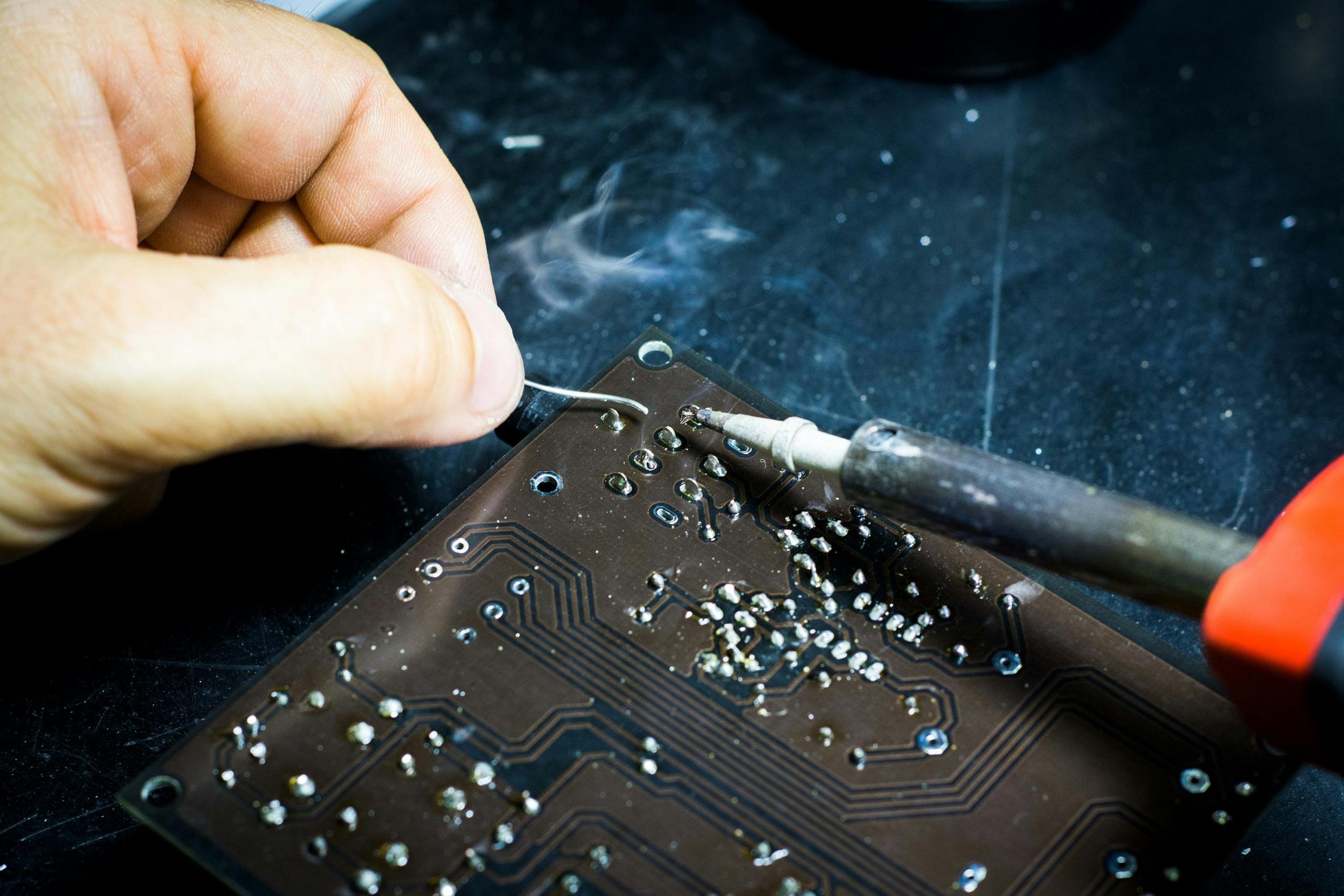
Technical Support for Climatic Chambers
The climatic chamber is an extremely complex laboratory tool, equipped with high-tech electronic components and sensors.
High quality climatic chambers are instruments designed to last several years and do not require much maintenance and/or frequent technical assistance.
However, as any other electronic device, the life cycle of the product depends mainly on the use we made of it, therefore both on the way we use it and how often we use it, as well as on environmental and/or random factors, which are obviously not under our control.
Vediamo ora quali possono essere le motivazioni per cui potrebbe essere necessario richiedere assistenza per una camera climatica. Possono essere raggruppati in tre macro-categorie:
- installation and first use (testing)
- ordinary maintenance (e.g. filter replacement)
- extraordinary maintenance
Installation and first use
Installing a climatic chamber is basically a simple process for an experienced laboratory technician. The manufacturer of climatic chambers must provide a detailed user manual indicating exactly how to install the instrument and how to manage the first use.
Although, this does not always turn out to be successful. It is not uncommon, even for a laboratory expert, to deal with such instruments for the first time and therefore run into common mistakes. It might happen, for example, an incompatibility between the voltage of your laboratory and the one required for the machine’s operation. This error, in the worst case scenario, can lead to the failure of the electronics of the equipment.
Ordinary Maintenance for Climatic Chambers
The ordinary maintenance of the climatic chamber is necessary to ensure its correct functioning and to extend the life cycle of the equipment as much as possible.
Among the most common ordinary maintenance interventions, we can mention:
- Keeping the inside of the chamber and its condenser cleanit is good practice to clean the inner parts of the tool as often as possible. This can be carried out by the same laboratory technician that uses the equipment. The interior of the FDM climatic chambers, available in stainless steel, facilitates this procedure.
- Keeping the water clean: most of the environmental chambers available in the market can be connected directly to the laboratory water supply using tap water, as these machines are equipped with a filter that purifies the water. Alternatively, they can be equipped with an external tank which, however, requires demineralized water. All FDM chambers provide both solutions.
- Replacing the water filterdirectly connected to the previous point, it is the most important intervention for a chamber with temperature and humidity control.
As well highlighted in the user manuals of FDM products, the replacement of the water filter must be carried out every 4, maximum 6 months, according to the frequency of use, to avoid the formation of calcium in the parts containing water and therefore malfunctions to the humidification system.
Extraordinary Maintenance for Climatic Chambers
Some cases, however, imply the need for support from a qualified technician for possible failures and malfunctions, which, as with any other instrument, can also be unpredictable. The components that could require such interventions are mainly:
- Water filling valve, which, in the event of unclean water, can leak and not close properly
- Humidification system:
- Fans
- Temperature and/or humidity probe
Real-Time Technical Support for Climatic Chambers
Real-time technical support is extremely important, as there are tests to be performed within a specific deadline.
Let us see below how the FDM team manages the issue of technical assistance for climatic chambers and all our other products.
Remote FDM Technical Assistance
FDM was born at the end of the 40s as a family business: over the years, the know-how that we have acquired, has allowed us to grow and become a landmark, in Italy and around the world, for the climate control of environmentsHowever, our approach as a small family business, in relation to direct contact with our customers, has never changed.
The elephant management processes, typical of large companies, are not part of our approach, both in terms of the prompt response we provide to each request for information and in terms of technical support requests.
The Technical Assistance Service of the FDM Climatic Chambers, provides an important support in real time.
The system, Safe.Lab, by FDM, allows technicians to perform a quick check of the operation of the device anywhere in the world remotely.
This initial support is completely free, and will allow you to:
- Accelerate the dynamics that generates the malfunction
- Receive a feedback by 36h
- Fast and efficient support
Do you need Technical Assistance?
Contact us through the online technical support form: a member of the FDM team will take care of your request in real time and will process it within a maximum of 24 hours.
On-site FDM Technical Support
Although, sometimes it will not be possible to process a support request remotely, so an on-site intervention will be required.
No problem: we have a network of qualified technicians in practically every part of Italy and abroad. Even in case of on-site intervention, times and costs will be contained, with no surprises.
Our qualified assistance, constantly updated through periodic training on the equipment, will certainly know how to identify the causes of the issue of your chamber.
Official FDM spare parts will be provided to be able to carry out any climatic chamber repairs and restore the operation of any device.
Choosing an FDM climatic chamber, means choosing a team that will always provide maximum transparency and professionalism.
With FDM you will never have the feeling of dealing with a brand, but with people who do care about your laboratory research.
Are you looking for Technical Assistance?
Write to FDM Technical Support or Open the Chat