Climatic Testing for Electronics
Tests for end products in the electronics industry can cover different types of equipment and as many fields of application.
Climatic tests for electronic products, in particular, are mainly connected to IEC/EN 60068 standard and its branches, such as:
Both refer to environmental testing with controlled temperature and humidity, adjustable according to different requirements mentioned in the standard.
The electronics industry is characterised by tests with extreme conditions and sudden temperature and humidity variations, typical of military, automotive and aerospace applications.
Specific to the military sector, we have in fact another set of standards which are:
Let's see why in the next paragraphs.
Perform
Extreme Testing
Discover the new series of Environmental Chambers for controlled climate testing
Environmental Testing on Electronic Boards
In addition to simple consumer electronics products, electronic boards are mainly used in the automotive, military, aeronautical and aerospace sectors. These are all applications in which the reliability of a component is essential, in order to manufacture totally safe and high-performance end products. The relative climatic tests must therefore be just as severe.
Climatic tests on electronic boards fall, in some cases, into the family of thermal shock tests.
Thermal shock can be stronger than the material's resistance to it and cause failures such as broken soldering or pins, thus "unmasking" any manufacturing faults in the electronic board: this is exactly the purpose of environmental testing.
The last step in testing a circuit board, so that it can be considered functional is the so-called burn-in test.
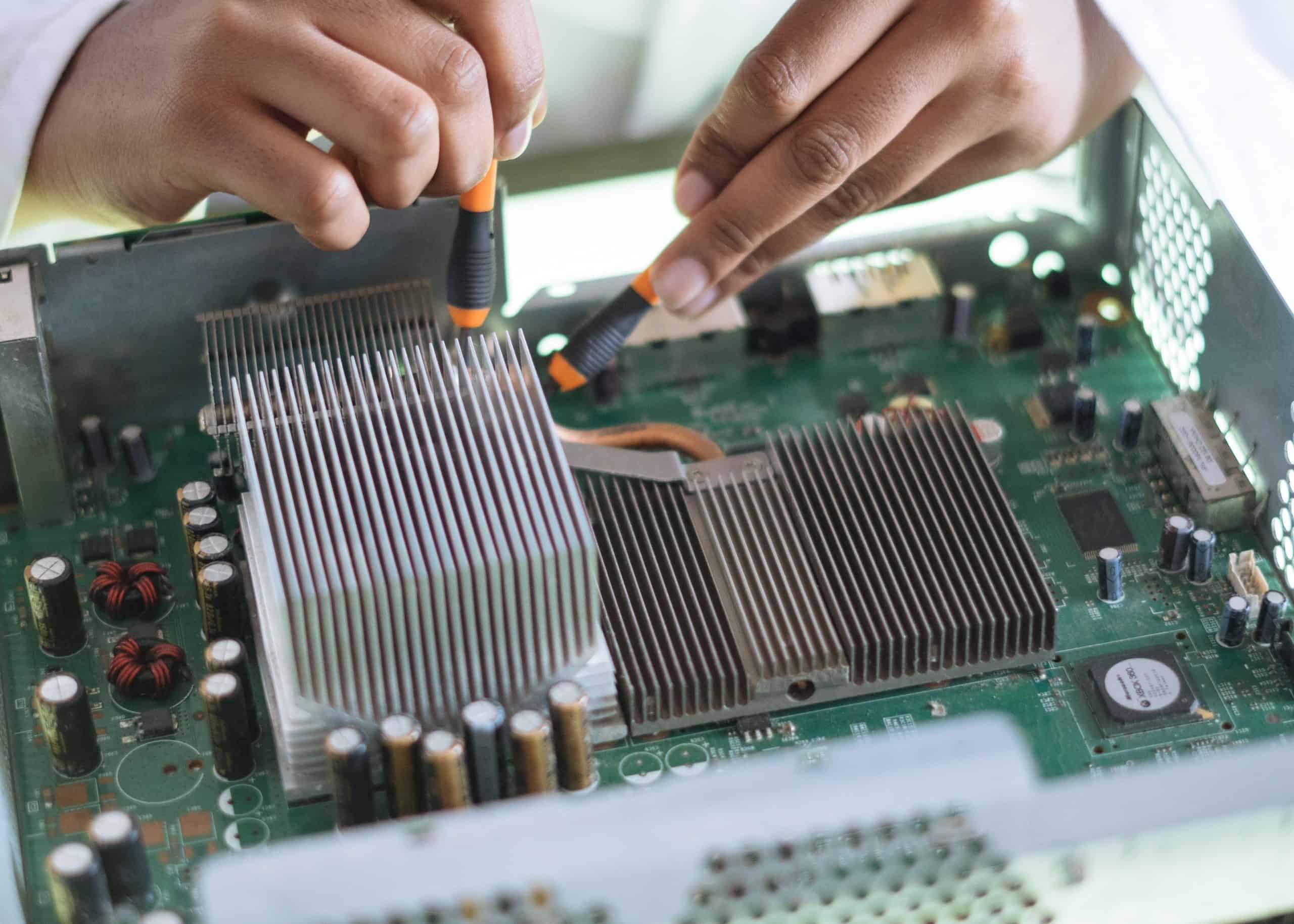
What is the Burn-in Test on Electronic Boards?
The burn-in test is a step in the testing of an electronic board: the burn-in is the final part of the test, together with the thermal cycling activities, both in the absence of bias and under operating conditions.
Burn-in, also known as HASS (Highly Accelerated Stress Screening) short-circuits all the components of the board through climatic stress. The testing temperature must be carefully controlled, not to be too high and burn out the chips, but high enough to simulate specific conditions.
A circuit board will have to deal with both standard and extreme environmental conditions during its life cycle.
Extreme temperature, however, is not only used to simulate an equally severe condition, but also to speed up standard conditions: we are talking about accelerated ageing tests.
Under normal conditions, it would take around 36 months to discover any defects in the board, and thus naturally replicating the characteristics of a burn-in test. The burn-in test, on the other hand, can be replicated in a limited time of about 170 hours, which fits perfectly into the industrial timelines of today's world.
The main objective of a burn-in test is to detect what is called infant mortality. If we think about it, the life cycle of a product is practically decided by the life of a single component, which can affect the total operation of the device.
Each element must therefore be studied in depth, in order to resolve any errors in advance and bring the infant mortality rate to zero.
The reasons why a electronic board may be defective are in the design or assembly and involve surface, metallisation and/or soldering defects.
The ideal situation of the so-called "bathtub" curve, presents infant mortality mainly in the initial phase, followed by a period of decline.
If each device is stressed for an x amount of time, the components with a high failure rate will be detected first and immediately eliminated.
If the test is successful and the board does not present any particular defect, the component is said to be "fit for purpose".
Online Configurator
Build a new Climatic Chamber
Environmental Chamber for Burn-in Tests
A climatic chamber for burn-in tests must therefore be able to guarantee the EUT (Equipment Under Test) sudden variations in temperature, and keep homogenous uniformity/stability of the parameters during the test.
Depending on the specific test requirement, some so-called thermal shock chambers (MIL-STD-883H No. 1010.8) subject the sample to extreme conditions, by switching from a so-called hot zone to a cold zone, within the same testing equipment.
The sudden temperature variations will bring to light all the parts related to infant mortality.
FDM Environmental Chambers
FDM environmental chambers, with a heating/cooling rate of respectively +5/-4°/min, are the ideal equipment for burn-in tests in electronics, but also automotive, military and aerospace.
This specification not only simulates real conditions to reveal the mortality of faulty components, but also reduces testing times, in order to meet today's industrial R&D timescales.
The internal temperature is homogeneous in all parts of the chamber, to avoid dispersion of any kind.
With a temperature range of up to -70/180°, adjustable humidity up to 98°, and a volume range starting at 25 litres, FDM environmental test chambers provide a solution for every requirement in the field of climatic testing for electronics.
Would you like to receive a quote or do you have questions about the product?
Contact us to receive more information about this Product.